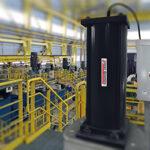
Cowan Dynamics
This article has been reviewed by Cowan Dynamics Application Engineering team. Contact Us and our application engineers will assist you with your application.
Flotation cells are mechanical equipment that bring the ore in contact with air, water, and chemical agents. Their main function is to separate the previously conditioned slurry into a concentrate and tailings. The level of these cells is controlled by dart valves, which in turn are operated by actuators. The calculation of the level control valve (Dart) in flotation cells requires high consideration as the goal is accurate flow control to maximize slurry retention time and minimize downtime, therefore a reliable and accurate control valve actuator is essential.
Traditionally dart valves use mechanical connections to feed position feedback to positioners that are then used to operate the actuators. The mechanical connections or arms, because they are exposed, are easily jammed, loosened, or damaged, resulting in a loss or compromise of position feedback and consequently a loss of control of the dart valve. This leads to accelerated valve and actuator wear and poor process control.
Cowan Dynamics has designed and patented a solution to this problem, conventional connecting arms are replaced by a transducer completely contained within the pneumatic actuator of the dart valve, eliminating mechanical connections. As a result, performance is maximized through optimized valve control and reduced maintenance, as the transducer is protected from the aggressive external environment. This solution is offered in the AT Series of actuators for control.
How do we eliminate mechanical connections?
The cable-type transducer provides a signal proportional to the stroke position, this electrical feedback is fed directly to the positioner. The transducer design is modular, making it easily accessible for maintenance and replacement in the field.
This solution for optimized control of dart valves is complemented by the pneumatic control panel to not only obtain local and remote control, but to protect the accessories from environmental contamination.