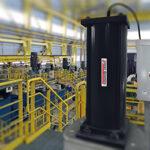
Cowan Dynamics
This article has been reviewed by Cowan Dynamics Application Engineering team. Contact Us and our application engineers will assist you with your application.
What is a gate valve?
Gate valves are linear valves where the closing membrane is a wedged disc or gate which moves perpendicular to the flow, allowing more flow as it moves away from the seat. These valves usually have metal seats and are bi-directional, the gate is wedged into the seat for which reason they are thrust seated valves. Gate valves are designed to be used as isolation or on/off valves therefore, are usually in a fully open or fully closed position. Normally in industry, they are flanged but also are offered in other connections such as threaded or welded.
Gate Valve Applications
They are often found at the end of pipelines where they serve as a final barrier against leaks before connecting into other pipelines or tanks, also very commonly used as isolation valves to do maintenance on other piping equipment such as pumps or control valves. Because of their seat design, they are used in extreme temperature applications and this makes the gate valve very useful in applications in chemical plants, oil refineries, mining processing, etc.
Gate Valve Advantages
- Gate valves contain very low friction loss because they do not obstruct the passage of fluid when fully open. This helps to save energy and reduce operating costs.
- Are available in large sizes
- Easy to maintain and disassemble and are relatively inexpensive
- Can be used with slurries and viscous liquids
- Bidirectional
- Most wedge gate valves are metal seated which allows them to be used in high-temperature applications.
Gate Valve Disadvantage
- They have slow open and close times due to their linear opening characteristic.
- Gate valves are difficult to repair since the valve seating surfaces are complex
- In systems where high-temperature changes rapidly, due to the load in the pipe at the valve end, leakages in gate valves occur.
- They have a large design, so they are heavy valves and need good mechanical support in the pipeline.
- Higher costs compared to valves of a more compact design.
- Most gate valves are metal seated, which affects the ability to provide tight shutoff
Gate Valve Actuators
The gate valve has a long history and the first valve patent ever issued was for a gate valve in 1840. In those times, steam was used to control the actuation movement. This long history makes for a technology that has not seen much change but has an extremely important function for industrial process control.
Gate valves, like any other type of valve, need an energy source to be operated. The energy required depends mainly on the design and the pressure differential across the valve. Gate valve actuators can be selected depending on the source of power (hydraulic, pneumatic, electric, etc.) to the actuator.
When pneumatic pressure is available, gate valve actuators can be:
Double-Acting Valve Actuator, for double-acting actuation
Spring-Return Valve Actuator, for single-acting actuation
When hydraulic pressure is available, gate valve actuators can be:
Double-Acting Hydraulic Actuator, for double-acting actuation
Spring-Return Valve Actuator, for single-acting actuation
When electric power is available:
Electro-hydraulic Linear Actuator, for double and single acting actuation