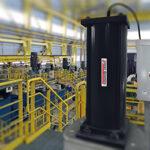
Cowan Dynamics
This article has been reviewed by Cowan Dynamics Application Engineering team. Contact Us and our application engineers will assist you with your application.
We’ve put together this article to help readers gain a comprehensive understanding of valve types, their functions, and selection criteria. This guide is ideal for engineers, maintenance professionals, and industry specialists who need to understand valve selection and operation for industrial and commercial applications.
Specifically, it will cover:
- Fundamentals of Valves – Explaining what valves are and their role in controlling fluid flow in various industries.
- Key Components of Valves – Breaking down the essential parts of a valve, including the valve stem, closing membrane, valve body, and valve seat.
- Types of Valves and Their Applications – Providing an overview of different valve types, such as gate, ball, butterfly, plug, check, diaphragm, and control valves, along with their specific uses.
- Selection Criteria for Valves – Offering guidance on choosing the right valve based on factors like fluid type, pressure and temperature conditions, and flow control needs.
- Material Considerations – Explaining how different materials (e.g., stainless steel, brass, PTFE) affect valve durability and performance.
- Valve Actuation – Comparing manual and automatic valve actuation methods, including pneumatic, hydraulic, and electric motor actuators.
- Flow Control and Pressure Regulation – Exploring how valves regulate upstream and downstream pressure while ensuring optimal system performance.
- Manual vs. Automatic Valves – Discussing the advantages, disadvantages, and best-use cases for manual and automated valve systems.
What Are Valves?
Valves are essential mechanical devices designed to control flow by opening, closing, or partially obstructing fluid flow in a piping system. They range in size from fractions of an inch to 360 inches and can be found in everyday applications such as plumbing, as well as in highly specialized industries like nuclear power.
Key Components of Valves and Their Functions
Regardless of the type of valve, all valves share four fundamental components that enable them to control fluid flow effectively. Understanding these components is essential for selecting the right valve for an application and ensuring its proper operation and maintenance.
Valve Stem
Function:
- The valve stem acts as the mechanical link between the actuator (manual handle, electric motor, pneumatic or hydraulic actuator) and the closing mechanism of the valve.
- It transfers the force applied by the operator or actuator to engage or disengage the closing membrane.
- The movement of the stem can be linear (as in gate and globe valves) or rotational (as in ball, plug, and butterfly valves).
Types of Valve Stems:
- Rising Stem: The stem moves up and down as the valve opens and closes, providing a visual indication of valve position (e.g., gate valves).
- Non-Rising Stem: The stem remains in place while an internal threaded mechanism moves the closing element (common in space-restricted applications like underground pipelines).
- Rotary Stem: Used in quarter-turn valves, where the stem rotates rather than moves linearly (e.g., ball and butterfly valves).
Materials:
-
Typically made from stainless steel, carbon steel, or brass, depending on operating conditions such as temperature, pressure, and exposure to corrosive fluids.
Closing Membrane
Function:
- The closing membrane (also called the closure element, disc, or obturator) directly controls the flow of fluid through the valve.
- When engaged, it creates a barrier that prevents fluid movement; when disengaged, it allows fluid to pass.
Types of Closing Mechanisms:
- Gate (Wedge or Parallel Disc): Used in gate valves for full flow or complete shut-off.
- Ball: Spherical component with a hole that aligns with the flow when open (ball valves).
- Butterfly Disc: A rotating disc used in butterfly valves to throttle or stop flow.
- Diaphragm: A flexible membrane used in diaphragm valves to create a seal.
- Plug: A cylindrical or tapered component used in plug valves.
- Poppet: Used in check valves to prevent backflow.
Materials:
-
Typically made from stainless steel, brass, PTFE (Teflon), rubber, or ceramic, depending on application requirements like pressure, temperature, and fluid compatibility.
Valve Body
Function:
- The valve body (also called the shell) is the outer casing that houses all internal components and contains the fluid under pressure.
- It determines the valve’s strength, pressure capacity, and durability.
Common Body Materials:
- Cast Iron & Ductile Iron – Used in water distribution and HVAC systems.
- Carbon Steel – Suitable for high-pressure and high-temperature industrial applications.
- Stainless Steel – Resistant to corrosion, used in chemical processing and food industries.
- Bronze & Brass – Used in marine, plumbing, and low-pressure applications.
- PVC & CPVC – Lightweight, corrosion-resistant materials used in water treatment and chemical handling.
Body Configurations:
- Straight-Through Flow: Minimal resistance to flow (gate, ball, and plug valves).
- Angle Flow: Redirects flow at 90 degrees (angle globe valves).
- Multi-Port: Allows flow in multiple directions (multi-port ball valves).
- Valve Stem: Transfers energy from the operator to the closing membrane.
- Closing Membrane: Blocks the fluid flow when engaged.
- Valve Body: The main pressure-containing envelope of the valve.
- Valve Seat: Positioned between the body and closing membrane to ensure a secure shut-off.
Valve Seat
Function:
- The valve seat is the sealing surface that ensures a leak-tight closure between the closing membrane and the valve body.
- It prevents fluid from passing through when the valve is in the closed position.
Types of Valve Seats:
- Soft Seat: Made of materials like PTFE, rubber, or plastic. Provides a tight seal but is less resistant to high temperatures and aggressive chemicals.
- Metal Seat: Made of stainless steel, bronze, or other alloys. Used in high-temperature, high-pressure, and abrasive environments.
- Resilient Seat: Combines a metal structure with a soft-sealing material for enhanced durability and sealing efficiency.
Applications:
- Soft-seated valves (e.g., PTFE-lined ball valves) are used in chemical industries where leak prevention is critical.
- Metal-seated valves (e.g., high-pressure gate valves) are preferred in steam, oil, and gas applications where extreme conditions exist.
Summary Table: Valve Components and Their Roles
Component |
Function |
Common Materials |
Common Valve Types |
---|---|---|---|
Valve Stem |
Transfers force from operator/actuator to closing membrane |
Stainless Steel, Carbon Steel, Brass |
Gate, Globe, Ball, Butterfly, Plug, Diaphragm |
Closing Membrane |
Blocks or allows fluid flow |
Stainless Steel, PTFE, Rubber, Ceramic |
Gate (Wedge), Ball, Butterfly Disc, Plug, Diaphragm |
Valve Body |
Encloses internal parts, withstands pressure |
Cast Iron, Carbon Steel, Stainless Steel, Bronze, PVC |
All valve types |
Valve Seat |
Provides a sealing surface for closure |
PTFE, Stainless Steel, Rubber, Ceramic |
Ball, Gate, Globe, Butterfly, Check |
Types of Valves and Their Functions
Valves are classified based on their application, operating mechanism, and flow control characteristics. The two different groups types of valves include isolation valves & control valves.
Isolation Valves (ON/OFF Valves)
Used when the primary function is to either fully permit or block fluid flow. These are commonly found in maintenance and repair applications to isolate sections of a piping system.
Examples of 6 Types of Valves:
- Gate Valves – Suitable for straight-line flow with minimal pressure drop.
- Ball Valves – Quarter-turn valves ideal for quick shut-off.
- Butterfly Valves – Compact, lightweight, and cost-effective for high-flow applications.
- Plug Valves – Ensure minimal leakage and are good for slurry or corrosive services.
- Check Valves – Prevent backflow in a piping system.
- Diaphragm Valves – Used for hygienic applications and small diameter piping systems.
Gate Valves in Detail
Gate valves are linear motion valves designed for accurate flow control in applications requiring minimal pressure drop and unrestricted flow. Commonly used in industries like oil & gas, water treatment, power plants, and chemical processing, they feature a valve body that houses a sliding gate mechanism, allowing for regulated fluid flow with a tight seal when fully closed.
Available in materials like cast iron, stainless steel, and bronze, gate valves come in various sizes to accommodate different pipeline systems.
Ball Valves in Detail
Ball valves are essential for precise and reliable flow control in industries such as oil & gas, water treatment, chemical processing, HVAC, and pharmaceuticals.
They come in various types, including floating, trunnion-mounted, full port, reduced port, V-port, and multi-port designs, each suited for specific pressure and flow requirements. Made from materials like stainless steel, brass, carbon steel, PVC, and PTFE-lined options, they offer durability and resistance to corrosion.
Ball valves can be actuated manually (lever or gear-operated) or automated using pneumatic, electric, or hydraulic actuators, making them ideal for both simple and high-pressure applications.
Butterfly Valves in Detail
Butterfly valves are versatile flow control devices used across industries like water treatment, oil & gas, chemical processing, HVAC, and food production.
Their compact design and quick operation make them ideal for regulating various fluids, with material options ranging from cast iron to stainless steel, and sizes spanning from small (2 inches) to massive industrial-scale valves (100+ inches).
Available in wafer, lug, double-offset, and triple-offset types, they cater to different pressure and temperature conditions.
Control Valves
Designed to regulate flow, pressure, and temperature by modulating the passage of fluids.
Examples of 5:
- Globe Valves – Allow precise flow control with high-pressure capability.
- Needle Valves – Used for precise flow control in small diameter piping systems.
- Pinch Valves – Ideal for handling slurries and abrasive media.
- Pressure Relief Valves – Used for relieving pressure in systems with excessive build-up.
- Pressure Reducing Valves – Maintain a controlled output pressure from a higher inlet pressure.
Globe Valve in Detail
Globe valves are essential flow control devices widely used in industries such as oil & gas, water treatment, power generation, chemical processing, and HVAC.
Designed for precise throttling and flow regulation, globe valves offer excellent pressure control and sealing capabilities, making them ideal for applications requiring frequent adjustments and minimal leakage. They are available in a range of materials, including cast iron, carbon steel, stainless steel, and high-performance alloys, ensuring durability in demanding environments.
Globe valves come in T-pattern, Y-pattern, and Angle-pattern configurations, each suited for different flow and pressure conditions. With options for manual, pneumatic, and electric actuation, they provide flexibility for various industrial applications.
Selecting the Right Valve
When choosing a valve, consider the following factors:
- ✔️ Fluid Type: Corrosive, abrasive, clean water, or gases.
- ✔️ Operating Pressure & Temperature: High-pressure or low-pressure drop conditions.
- ✔️ Flow Path & Control Requirements: Straight flow, directional changes, or modulation.
- ✔️ Valve Actuation Needs: Manual operation, electric motor actuators, hydraulic or pneumatic systems.
Valve Construction and Material Selection
The selection of materials depends on the application environment:
- High-Pressure Applications: Require metal-seated valves.
- Corrosive Fluids: Stainless steel or exotic alloys.
- Cryogenic Applications: Low-temperature carbon steels such as ASTM A352 LCC.
- High-Temperature Applications: Chromium carbide or tungsten carbide coatings ensure durability.
Valve Actuators
Valves may be manually operated or automated using valve actuators:
- Manual Valves – Operated by handwheels or gearboxes.
- Pneumatic Actuators– Use air pressure to drive valve motion.
- Hydraulic Actuators – Utilize fluid systems like oil for actuation.
- Electric Motor Actuators – Employ electric motors to generate movement.
- Electrohydraulic Actuators – Combine electrical power with hydraulic systems.
Flow Control
Different types of valves are designed to manage pressurized liquids effectively while ensuring efficient flow direction and system performance. Butterfly valves, for example, offer low fluid resistance, making them ideal for applications requiring minimal pressure drop.
The ability to regulate upstream pressure and downstream pressure is crucial in maintaining stable flow conditions, especially in pipelines carrying high-pressure fluids. Some valves, like check valves, prevent reverse flow, protecting equipment and maintaining operational safety.
Valve size also plays a key role in flow control, with larger valves handling higher volumes of fluid while maintaining efficiency. Selecting the right valve type depends on the system’s pressure, required flow direction, and specific industry application.
Manual Valves vs Automatic Valves
Manual Valves
Manual valves are operated by hand using a lever, wheel, or gear. They require human intervention to open, close, or adjust the flow.
When to Use Manual Valves:
- When infrequent operation is required.
- When simple on/off control is sufficient.
- When automation is not justified due to cost or complexity.
- In low-risk applications where human intervention is acceptable.
Pros of Manual Valves: ✔️ Lower cost upfront and no need for power sources.
✔️ Simple and reliable operation.
✔️ Easier maintenance and repair.
✔️ Suitable for applications where adjustments are not frequent.
Cons of Manual Valves: ❌ Requires physical presence to operate.
❌ Prone to human error, leading to inconsistent control.
❌ Not ideal for precise or remote operation.
❌ Can be hazardous in extreme environments (e.g., high pressure, toxic fluids).
Automatic Valves
Automatic valves are operated by actuators (electric, pneumatic, or hydraulic) that allow remote or automated control without human intervention.
When to Use Automatic Valves:
- When remote or automated control is needed.
- When precise and consistent flow regulation is required.
- When safety is a concern (e.g., hazardous environments, high temperatures, toxic gases).
- In large-scale industrial applications where efficiency and response time matter.
Pros of Automatic Valves: ✔️ Enables remote and automated operation.
✔️ Provides precise and consistent control.
✔️ Enhances safety by reducing human exposure to dangerous environments.
✔️ Reduces labor costs by minimizing manual intervention.
✔️ Faster response time in critical applications.
Cons of Automatic Valves: ❌ Higher initial cost due to actuators and control systems.
❌ Requires a power source (electricity, air, or hydraulic pressure).
❌ More complex maintenance and repair.
❌ Potential for failure due to power loss or system malfunction.
Summary Chart: Choosing Between Manual and Automatic Valves
Factor |
Manual Valve |
Automatic Valve |
---|---|---|
Control |
Requires human operation |
Controlled remotely or automatically |
Precision |
Limited control |
High precision with automation |
Safety |
Risk of human exposure |
Minimizes human interaction in dangerous areas |
Cost |
Lower initial cost |
Higher cost due to actuators |
Maintenance |
Simple and easy |
More complex and requires technical expertise |
Speed |
Slower due to manual operation |
Fast response for quick adjustments |
Reliability |
Less prone to technical failure |
Can fail if power supply is lost |
Choosing The Right Actuator for your Valve
Selecting the right actuator for your valve is critical to ensuring optimal flow control, efficiency, and safety in industrial applications. From isolation valves like gate and ball valves to precision control valves such as globe and needle valves, each type serves a specific purpose depending on factors like pressure, temperature, fluid type, and actuation needs. Understanding valve components, materials, and operational mechanisms can help prevent failures, improve performance, and extend the lifespan of your systems.
At Cowan Dynamics, our team of experienced engineers specializes in helping industries select, customize, and integrate high-performance valve automation solutions tailored to their operational needs. Whether you require manual, pneumatic, hydraulic, or electric actuated valves, we provide expert guidance and cutting-edge automation technologies to enhance efficiency and reliability.
Need help selecting the right valve for your application? Contact Cowan’s engineers today to discuss your requirements and explore solutions that optimize your system’s performance.