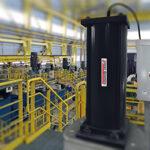
Cowan Dynamics
This article has been reviewed by Cowan Dynamics Application Engineering team. Contact Us and our application engineers will assist you with your application.
A globe valve is an essential components in industrial fluid control systems, offering precise flow regulation and reliable shut-off capabilities. Their design and functionality make them indispensable in large-scale applications, such as oil and gas, power generation, chemical processing, and water treatment.
This article explores the technical aspects of globe valves, including their design, sizes, parts, use cases, efficiency, maintenance requirements, and the types of actuators that work with them.
What is a Globe Valve?
A globe valve is a type of linear motion valve used to regulate, start, or stop fluid flow. The valve’s closure mechanism involves a movable plug or disc element and a stationary ring seat, typically arranged in a spherical body shape. Globe valves are named for their originally spherical shape, which contributes to their functionality in regulating flow. The valve body consists of two halves separated by an internal baffle. The plug is connected to a stem, which is operated by screw action or via an automated actuator. The name “globe valve” originates from the spherical bodies which gave them their distinctive shape, though modern designs may vary.
Globe valves are particularly valued for their ability to provide fine flow control and tight valve closure, making them ideal for applications requiring precise throttling. Their design allows for minimal leakage and high durability, even in high-pressure and high-temperature environments. The closure mechanism involves plugs that are typically solid and unbalanced, which helps minimize fluid clogging and corrosion.
Sizes Available
Globe valves are available in a wide range of sizes to accommodate various industrial needs. Sizes typically range from small diameters (e.g., ½ inch) for specialized applications to large diameters (e.g., 24 inches or more) for heavy-duty industrial processes.
In large-scale applications, such as power plants or oil refineries, globe valves with diameters exceeding 12 inches are common. These larger valves are often custom-designed to meet specific operational requirements.
Parts of a Typical Globe Valve
A globe valve comprises several key components, each playing a vital role in its operation:
- Valve Body: The outer shell that houses the internal components and connects to the pipeline. The valve body is often separated by an internal partition to guide fluid flow. In a straight body globe valve, the flow path is linear, which simplifies design and reduces turbulence. Globe valves are available with stainless steel trim for enhanced durability.
- Bonnet: The cover that seals the valve body and provides a housing for the stem.
- Stem: The rod that connects the actuator or handwheel to the movable plug or disc, enabling its movement. Many modern globe valves and automated globe valves use smooth stems to reduce friction and wear.
- Plug or Disc Element: The component that moves against the seat to regulate or stop flow. In globe valves, the plug or disc is critical for achieving tight valve closure. Unbalanced plugs, typically solid, are often used to ensure durability and reliability. Balanced plugs may feature holes through the plug itself.
- Seat: The stationary ring against which the plug or disc element seals to stop flow. The seat ring is a critical component that provides a stable, uniform shut-off surface.
- Gaskets: Sealing materials that prevent leakage between components.
- Packing: Material that seals the stem to prevent leakage along its movement path.
Each part of a globe valve must be precisely engineered to ensure optimal performance and longevity.
Use Cases
Globe valves are widely used in industries where precise flow control and reliable shut-off are essential. Some common use cases include:
Power Plants: Regulating steam and coolant flow in turbines and boilers. Globe valves are particularly suited for steam applications because they can handle high temperatures and pressures while providing precise control.
Oil and Gas: Controlling the flow of crude oil, natural gas, and refined products.
Chemical Processing: Managing the flow of corrosive or hazardous chemicals. The design of globe valves helps minimize fluid clogging and corrosion, making them ideal for such environments.
Water Treatment: Regulating water and wastewater flow in treatment plants.
In these applications, the globe valve’s ability to handle high pressures and temperatures while providing precise control makes it a preferred choice.
Efficiency
The efficiency of a globe valve is determined by its ability to minimize pressure drop, provide tight valve closure, and offer precise flow control. While globe valves are highly effective for throttling, they typically introduce a higher pressure drop compared to other valve types, such as ball valves. This is due to the tortuous flow path created by the valve’s design.
However, advancements in globe valve technology, such as improved seat and plug or disc element designs, have significantly enhanced their efficiency. These are engineered to reduce pressure drop and improve flow characteristics, making them more energy-efficient in industrial applications.
Maintenance
Like any mechanical component, globe valves require regular maintenance to ensure optimal performance. Common issues that may arise include:
- Leakage: Often caused by worn-out gaskets, packing, or damaged seats. Worn-out seat rings can also cause leakage.
- Stem Corrosion: Exposure to corrosive fluids can degrade the stem over time.
- Disk and Seat Wear: Frequent operation can lead to erosion or pitting of the plug or disc element and seat. The seating surface is crucial in ensuring a leak-tight seal.
- Packing Failure: Improper installation or wear can cause packing to fail, resulting in leaks.
- Actuator Malfunction: In automated systems, actuator failure can prevent the valve from operating correctly.
Regular inspection, lubrication, and replacement of worn parts are essential to prevent these issues and extend the lifespan.
What Type of Actuators Work?
Globe valves can be operated manually or automatically using actuators. The choice of actuator depends on the application’s requirements, such as the need for remote operation, precision, or speed. Common types of actuators used with globe valves include:
Electro-Hydraulic Actuators
An electro-hydraulic actuator (EHA) operates the globe valve by converting electrical signals into hydraulic motion, which then mechanically moves the valve stem to control fluid flow. Ideal for precise control and automation, electro-hydraulic actuators are commonly used in power plants and water treatment facilities.
Double and single acting linear electrohydraulic for isolation and controls, Cowan Series E2H
Pneumatic Actuators
These use compressed air to operate the valve and are suitable for applications requiring fast response times. A globe valve with pneumatic actuator is often used in industries where quick valve operation is critical.
Double-acting linear pneumatic actuators, Cowan Series A
Single-acting linear pneumatic actuators, Cowan Series AS
Single and double-acting linear pneumatic actuators for control, Cowan Series AT
Single and double-acting linear pneumatic actuators for control, Cowan Series CDA
Hydraulic Actuators
Known for their high force output, hydraulic actuators are used in heavy-duty applications, such as oil and gas pipelines.
Double-acting linear hydraulic actuators, Cowan Series ML
Single-acting linear hydraulic actuators, Cowan Series MS
Manual Actuators
Handwheels or levers are used for manual operation in smaller or less critical applications.
Additionally, a globe valve with position indicator can provide real-time feedback on the valve’s status, which is particularly useful in automated systems.
Associations & Standards
There are several industry associations that oversee, regulate, or provide standards for globe valves and other types of industrial valves.
- American Society of Mechanical Engineers (ASME) – Sets codes and standards for valves, including ASME B16.34 for pressure-temperature ratings. www.asme.org
- American Petroleum Institute (API) – Develops standards for valves used in oil, gas, and petrochemical industries, such as API 602 for compact globe valves. www.api.org
- Valve Manufacturers Association of America (VMA) – Represents North American valve manufacturers and provides industry insights. www.vma.org